CALL US
EMAIL US
Engineering Precision Ceramics
Engineering Ceramics are structured ceramics whose physical properties are optimized for industrial applications in various stages of manufacturing such as Shaping, Sintering and Finishing.
We offer Engineering Precision Ceramics with Purities ranging from 86.00% to 99.99%. To satisfy our customers’ requirements, purity and composition of ceramics are manufactured as required and delivered according to their specifications. Engineering Ceramics typically have good temperature resistance capabilities greater than 2000 °C and other inherent characteristics such as minimal wear rates, non-corrosiveness and being electrically insulative.
The general properties of ceramic materials present the following advantages:
- Controlled Microstructures / High Purities
- High Uniformity with High Tolerances Control / Machined
- Polished / Near Net Shape Processing
- Low Particles Generation
- Excellent Wear / Abrasion Resistance
- Excellent Dielectric Properties
- Chemically (Acidic & Alkaline) Inert
- Good Thermal Conductivity
- Excellent Size and Shape Capability
- High Strength and Stiffness
- Excellent Fracture Toughness
- Excellent Impact Resistance
With such properties, Engineering Ceramics are best suited to be used in the following areas of applications:
- Dielectric Strength
- Electrical Isolation
- High Temperature Exposure
- Corrosive Environment
- Chemicals and Gases
- Thermal Shock
- Liquid and Gas Permeable / Impermeable
- Thermal Expansion Match
- Electro-Statics Dissipation
- Thin Film Deposition
We offer Engineering Ceramics with Purities ranging from 86.00% to 99.99%. To satisfy our customers’ requirements, purity and composition of ceramics are manufactured as required and delivered according to their specifications.
Product Forms
- Sputtering Targets
- Wafers Processing Tools
- Semiconductors Processing Tools
- Electronics / Mechanical Processing Tools
Typical Engineering Ceramics
- Aluminium Oxide (Al2O3)
- Zirconia Oxide (ZrO2)
- Zirconia Toughened Aluminium Oxide (ZTA)
- Silicon Nitride (Si3N4)
- Silicon Carbide (SiC)
- Boron Nitride (BN, PBN)
- Aluminium Nitride (AlN)
- Machinable Ceramics (MACER)
- ESD Zirconia (ZrO2) – Specifications will be provided upon request
- ESD Alumina (Al2O3) – Specifications will be provided upon request
- Porous Alumina (Al2O3)
ESD Ceramics are Electrostatic Dissipative materials that dissipate charges to ground in a slower and more controlled manner than with conductive materials. ESD Ceramics are used for the manufacture of precision automation and production tools, fixtures and product components where static charges and particle contamination must not be present.
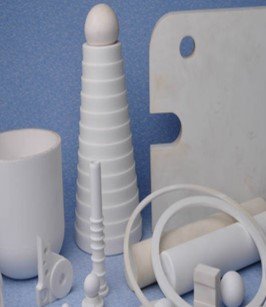
Typical Engineering Ceramics Grades and Specifications
Engineering Ceramics Grades | Unit | Al2O3 | Al2O3 | Zr2O2 | Zr2O2 | Zr2O2 | ZTA | Si3N4 | SiC | BN | AlN | MACER |
Colour | – | White / Ivory | White / Ivory | White | Yellow | White | White | Grey / Black | Grey | White | Grey | White |
Density | g/cm3 | 3.7 | 3.9 | 6 | 5.7 | 6 | 4.1 | 3.2 | 3.1 | 1.95-2.00 | 3.3 | 2.58 |
Flexural Strength | MPa | 300 | 390 | 800 | 700 | 1,100 | 600 | 750 | 410 | 30 | 420 | 108 |
Compressive Strength | MPa | 3,400 | 3,900 | 3,000 | 2,500 | 2,500 | 3,600 | 2,500 | 2,600 | 58 | NA | 488 |
Young’s Modulus of Elasticity | GPa | 350 | 390 | 205 | 200 | 200 | 350 | 320 | 410 | NA | 320 | 65 |
Impact Resistance | MPa.m1/2 | 4.0 | 5.5 | 8 | 7 | 11 | 7.5 | 6.7 | 3.2 | NA | NA | NA |
Weibull Modulus | M | 10 | 12 | 15 | 18 | NA | 15 | 15 | 10 | NA | NA | NA |
Vickers Hardness | HV 0.5 | 1,800 | 2,000 | 1,150 | 1,200 | 2,200 | 1,600 | 1,650 | 2,500 | NA | 8 Moh’s | 4 – 5 Moh’s |
Thermal Expansion Coefficient | 10-6 K-1 | 5.0 – 8.3 | 5.5 – 8.5 | 10 | 10 | 10.5 | 6.0 – 8.6 | 3.4 | 4.0 – 5.8 | 1.5 | 4.4 – 4.8 | 8.6 |
Thermal Conductivity | W/m.K | 24 | 30 | < 2 | < 2 | NA | 18 | 22 | 110 | 30 | 180 | 1.68 |
Thermal Shock Resistance | ΔT°C | 250 | 280 | 270 | 250 | 300 | 320 | 750 | 350 | NA | NA | NA |
Maximum Use Temperature | °C | 1,600 | 1,700 | 1,000 | 1,000 | 1,000 | 1,000 | 1,300 | 1,500 | 900 – 2,100 | NA | 750 |
Volume Resistivity @ 20 °C | Ω·cm | >1014 | >1015 | >1010 | >1010 | >1012 | >1013 | >1011 | NA | >1014 | >1014 | >1014 |
Dielectric Strength | kV/mm | 20 | 30 | NA | NA | NA | NA | 20 | NA | NA | 17 | 40 |
Dielectric Constant | εr | 10 | 10 | NA | NA | NA | NA | NA | NA | NA | 8.9 | NA |
Dielectric Loss Angle @ 20°C, 1MHz | tanδ | 0.0001 | 0.0005 | NA | NA | NA | NA | NA | NA | NA | 2.8 x 10-4 | NA |
Typical Engineering Ceramics Porous Grades and Specifications
Properties | Unit | Porous Al2O3 |
Al2O3 | WT % | 82 – 84 |
SiO2 | WT % | 16 – 18 |
Density | g/cm3 | 2.3 – 2.5 |
Hardness | HRA | 50 |
Flexural Strength | MPa | 40 |
Compressive Strength | MPa | 600 |
Porosity | % | 40 |
Pore Size | µm | 30 – 60 |
Operating Pressure | MPa | 10 |
Acid Resistance | mg/cm2 | 10 |
Alkali Resistance | mg/cm2 | 20 |
Micro-Precision Manufacturing Process Capabilities
Given its ability to withstand high heat under applications, industries such as Telecommunication, Hard Disk Drives, Semiconducting Manufacturing and Electro-Mechanical Parts & Assemblies require ceramic parts to be Micro-Precision Manufactured.
We offer a wide array of Precision Machining capabilities such as Grooving, Slicing, Grinding, Lapping & Polishing.
Slicing Process Capabilities:
- Multiple Wire Saw Machines (Free Abrasives Machining)
- Wire Diameter 0.07 – 0.20 mm
- Work Size Typical 80 x 85 x 90 mm
- Slicing Thickness 0.10 – 1.00 mm
- Materials include Ceramics, Ferrous and Non-Ferrous
- Thickness Tolerances +/- 0.015 mm
Grooving, Slicing, Grinding, Lapping & Polishing
- Work Sizes 150 x 150 mm
- Work Piece Thicknesses 0.30 – 4.00 mm
- Final Part Sizes 0.500 x 0.500 mm
- Diamond Blade Thickness of 0.10 – 1.00 mm
- Standard Working Tolerances of ± 0.10 mm
- Lapping to Thickness 0.070 mm with tolerance of ± 0.002 mm
- Typical abrasives GC (Green Silicon Carbide) / WA (White Alumina)
- Surface Finish: 0.2 – 0.6 µm Lapped / < 0.0254 µm Polished